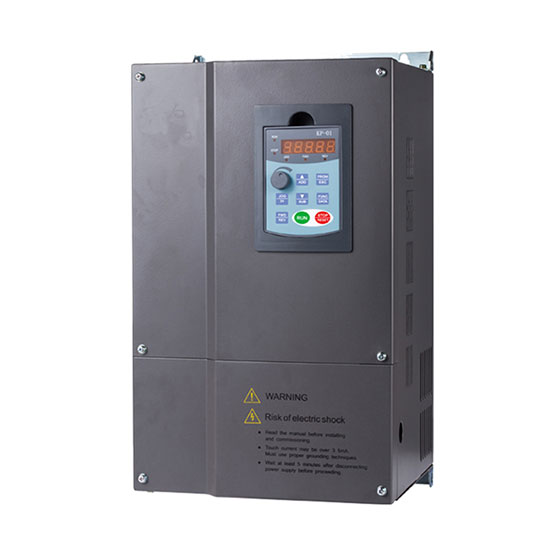
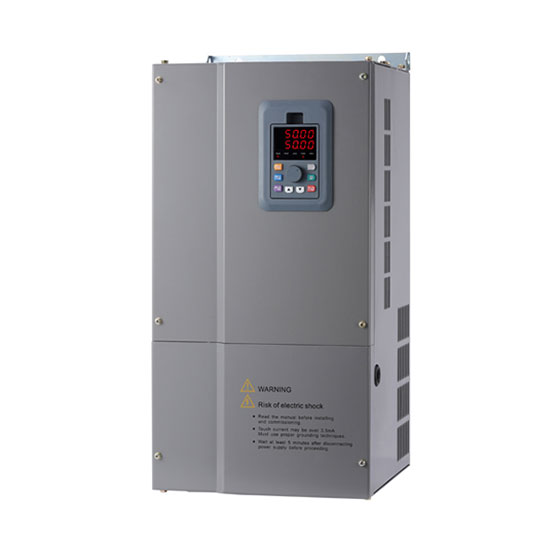


- Stock: In Stock
- Model: PEACO-FC280-4T-132G/160P
- SKU: PEACO-4T-TVFD-132160
Available Options
New style variable frequency drive for 3 phase motor features 175 hp (132 kW) rated capacity with phase voltage 220V to 1140V. High efficiency 3 phase AC drive is used to control the speed of an electrical motor by varying the frequency and voltage of its power supply. Our VFDs have operating features such as input/output terminals, RS485 communication interface, PID control, and jog operation. It is suitable for all kinds of AC induction motors used in various applications.
Navigation: Motor Controls > Variable Frequency Drives > Three Phase VFD > 175 hp (132 kW) VFD, 3 Phase AC Drive
Basics | Model | PEACO-FC280-4T-132G/160P | |
Rated Capacity | 175 hp (132 kW) | ||
Rated Input Current | 256A (for 380V) | ||
Rated Output Current | 253A (for 380V) | ||
Certification | CE | ||
Warranty | 12 months | ||
Applicable Motor Output | 132 kW | ||
Power | Input Rated Voltage* | 220V/380V/660V/1140V (-15%~+20%) & 460V/480V |
|
Output Rated Voltage* | 220V/380V/660V/1140V (-15%~+20%) & 460V/480V |
||
Rated Frequency | 1.0~3200Hz | ||
Robust Design | IGBT current > 2 times of inverter output current, Capacitor > 50uF/A | ||
PCB aging test | 100% test, 50°C, 12 hours. | ||
Finished products aging test | 100% test, 50°C, 24 hours. | ||
Control Feature | Control System | VF Control / Open Sensor Vector Control / Closed loop Vector (PG card) | |
Output Frequency Resolution | 0.1Hz | ||
Torque Characteristics | Including the auto-torque, auto-slip compensation, starting torque can be 0.5 Hz/150% (V/f), 1 Hz/150% (SVC),0 Hz/180% (FVC) | ||
Overload Endurance | 150% / 120s, 160% / 60s, 180% / 10s, 200% / 1s | ||
Acc / Dec Time | 0.1~65000s. (can be set individually) | ||
Torque Boost | Automatically torque boost, manually torque boost: 0.1%~30.0% | ||
Stall Prevention Level | 20~200%, setting of Rated Current | ||
Operating Feature | Input / Output Terminals | Keypad | Removable |
Input terminals | 6 multifunctional inputs, one can work as high-speed pulse Input. 3 programmable analog input: AI1, AI2, AI3: 0~10V / 4~20mA. |
||
Output terminals | 2 Groups relay outputs, 1 open collector outputs. 2 Analog outputs, 0~10V / 4~20mA. |
||
Communication Terminals | Build-in standard RS485 communication interface. MODBUS-RTU communication protocol. | ||
Built-in PID | Built-in PID control to easily realize the close loop control of the process parameters (such as pressure, temperature, flow, etc.) | ||
Jog Operation | Jog operation frequency: 0.0Hz~maximum frequency. Jog acceleration/deceleration time: 0.1s~3600.0s. | ||
Other Function | AVR, S-curve, Over-Voltage Stall Prevention, DC Braking, Fault Records, Adjustable Carried Frequency, Starting Frequency Setting of DC Braking, Over-Current Stall Prevention, Momentary Power Loss Restart, Reverse Inhibition, Frequency Limits, Parameter Lock/Reset. | ||
Protection | Over Voltage, Over Current, Under Voltage, Overload, Electronic Thermal, Overheating, Self-testing. | ||
Others | Including EMC Filter (C2/C3 Standard) | ||
Cooling | Forced air-cooling | ||
Installation Location | Altitude 1,000 m or below, keep from corrosive gasses, liquid and dust. | ||
Ambient Temperature | -10°C~+40°C (Non-Condensing and not frozen) | ||
Storage Temperature | -20°C~+60°C | ||
Ambient Humidity | Below 90% RH (non-condensing) | ||
Vibration | 9.80665m/s2 (1G) less than 20Hz, 5.88m/s2 (0.6Gat) 20 to 50Hz | ||
External Accessories |
Matched optional input EMC filter, output EMC filter, input AC reactor, output AC reactor, energy regenerated reactor, harmonic filter, and sine wave filter (excluding VFD price). |
1. The inverter can adjust the motor power and control the speed of an electrical motor to achieve electricity savings. For example, VFD is used for centrifugal fans and water pumps, the operator can control the speed easily according to needs to save energy.
2. VFD can reduce the voltage fluctuation in the power line and avoid the phenomenon of equipment tripping or abnormal operation once the voltage is abnormal.
3. The AC drive can reduce the impact on the power grid, thereby effectively reducing the reactive power loss and increasing the effective power of the power grid.
4. The frequency converter can also reduce the wear between the transmission parts in the machine, which also reduces the cost and improves the system's stability.
5. In addition, the variable frequency drive provides full functions, which can be well matched with other control equipment, so as to realize centralized monitoring and real-time control and solve many problems, including system compatibility for users.
- The first section of VFD (variable voltage control) not only converts the AC supply voltage into DC but also controls the required pulsating DC output voltage to maintain V/f constant ratio by using SCR/IGBT rectifier.
- The second section of VFD (DC-Link/DC Bus) consists of inductance and capacitors to convert pulsating DC into pure direct current. Here, inductance smooths the current, and the capacitor smooths the voltage.
- The third section of VFD (referred to as variable frequency control) not only converts DC voltage back into AC voltage but also controls the variable frequency to maintain the V/f ratio by using electronic devices such as SCR/IGBT transistors.
- Cooling method-forced air.
- Keep away the ac converter from corrosive gasses, liquid, moisture, and dust.
- Installation location altitude below 1000m (In the case above 1000m, VFD is to be de-rated. Please contact for technical support).
- Storage-temperate -20℃ to +60℃.
- Ambient temperature -10℃ to +40℃ (non-condensing and not frozen).
- Ambient humidity below 90% RH.
- Vibration under 20Hz 9.8m/s(1G), over 20Hz 5.88m/s (0.6G).
- V/f (volts per hertz) or V/hz control.
- V/f with encoder or closed loop V/f (PG card).
- Open loop vector control.
- Closed loop vector control (PG card).
- VFD capacity is to be sized more or equal to the sum of the capacity of all connected motors.
- The sum of the distance between the VFD and all connected motors should be less than 500m. Introduce an output load reactor to avoid motor failure due to voltage spikes, current surges, or harmonics.
- Install circuit breaker MCB or with extra protection MPCB between each motor and VFD.
- The voltage of each motor should be the same and ensure the VFD adoptable current is higher than the sum of all rated currents.
- Connect all motors with VFD output in parallel.