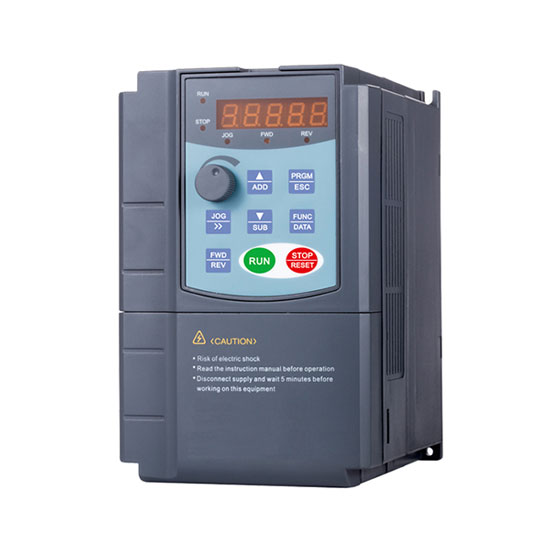
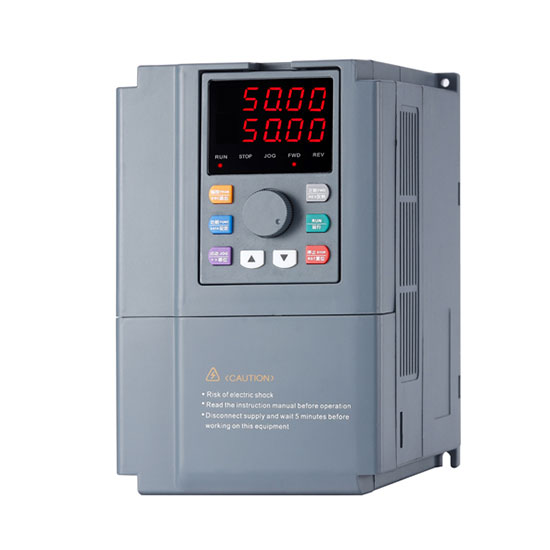


- Stock: In Stock
- Model: PEACO-1-FC280-2S/4T-0.75G/1.5P
- SKU: PEACO-VFD-1075
Available Options
Basics | Model | PEACO-1-FC280-2S/4T-0.75G/1.5P | |
Rated Capacity | 1 hp (0.75 kW) | ||
Rated Input Current | 8.2A | ||
Rated Output Current | 2.1A | ||
Certification | CE | ||
Warranty | 12 months | ||
Applicable Motor Output | 0.75kW | ||
Power | Input Rated Voltage* | Single phase AC 220 V (-15%~+20%) and Split voltage | |
Output Rated Voltage* | Three phase AC 380V (-15%~+15%) | ||
Rated Frequency | 1.0~3200Hz | ||
Robust Design | IGBT current > 2 times of inverter output current, Capacitor > 50uF/A | ||
PCB aging test | 100% test, 50°C, 12 hours. | ||
Finished products aging test | 100% test, 50°C, 24 hours. | ||
Control Feature | Control System | VF Control / Open Sensor Vector Control / Closed loop Vector (PG card - for lift/elevator) | |
Output Frequency Resolution | 0.1Hz | ||
Torque Characteristics | Including the auto-torque, auto-slip compensation, starting torque can be 0.5 Hz/150% (V/f), 1 Hz/150% (SVC),0 Hz/180% (FVC) | ||
Overload Endurance | 150% / 120s, 160% / 60s, 180% / 10s, 200% / 1s | ||
Acc / Dec Time | 0.1~65000s. (can be set individually) | ||
Torque Boost | Automatically torque boost, manually torque boost: 0.1%~30.0% | ||
Stall Prevention Level | 20~200%, setting of Rated Current | ||
Operating Feature | Input / Output Terminals | Keypad | Removable |
Input terminals | 6 multifunctional inputs, one can be work as high speed pulse Input. 3 programmable analog input: AI1, AI2, AI3: 0~10V / 4~20mA. |
||
Output terminals | 2 Groups relay outputs, 1 open collector outputs. 2 Analog outputs, 0~10V / 4~20mA. |
||
Communication Terminals | Build-in standard RS485 communication interface. MODBUS-RTU communication protocol. | ||
Built-in PID | Built-in PID control to easily realize the close loop control of the process parameters (such as pressure, temperature, flow, etc.) | ||
Jog Operation | Jog operation frequency: 0.0Hz~maximum frequency. Jog acceleration/deceleration time: 0.1s~3600.0s. | ||
Other Function | AVR, S-curve, Over-Voltage Stall Prevention, DC Braking, Fault Records, Adjustable Carried Frequency, Starting Frequency Setting of DC Braking, Over-Current Stall Prevention, Momentary Power Loss Restart, Reverse Inhibition, Frequency Limits, Parameter Lock/Reset. | ||
Protection | Over Voltage, Over Current, Under Voltage, Overload, Electronic thermal, Overheating, Self-testing. | ||
Others | Including EMC Filter (C2/C3 Standard) | ||
Cooling | Forced air-cooling | ||
Installation Location | Altitude 1,000 m or below, keep from corrosive gasses, liquid and dust. | ||
Ambient Temperature | -10°C~+40°C (Non-Condensing and not frozen) | ||
Storage Temperature | -20°C~+60°C | ||
Ambient Humidity | Below 90% RH (non-condensing) | ||
Vibration | 9.80665m/s2 (1G) less than 20Hz, 5.88m/s 2 (0.6Gat) 20 to 50Hz | ||
External Accessories* |
Matched optional input EMC filter, output EMC filter, input AC reactor, output AC reactor, energy regenerated reactor, harmonic filter, sine wave filter (excluding VFD price). |
1. * denotes the parameters are optional or customized and please select every parameter in drop-down lists to complete your order.
2. Please contact us for external accessories catalogue and price.
AC Drive Dimension (Unit: mm)
A | H | D | W | B | Φ | Weight |
118 | 185 | 157 | 106 | 175 | Φ4.5 | 2kg |
Control Circuit Diagram for Industrial Motor
Control Circuit Diagram for Lift or Elevator Motor
Variable frequency drive (VFD) is a very useful inverter, widely used in the field of industrial automation. It plays a greatly important role in improving industrial production efficiency and saving enterprise or personal costs. Variable frequency drive is a motor controller that changes the frequency and voltage supplied to the motor. Therefore, VFD is also called AC drive, AC frequency converter, variable speed drive.
Frequency (or Hertz) is directly related to the motor speed (RPM). In other words, the faster the frequency is, the faster the speed is. If the application does not require the motor to work at full speed, the VFD can be applied to reduce the frequency as well as voltage to meet the requirements of the motor load. Different applications have different motor speed requirements actually and the VFD can simply increase or decrease the speed of AC asynchronous motors to meet the speed requirements, can realize the soft start of the motors and improve the operation accuracy. The variable frequency drive also has the overcurrent, overvoltage, overload protections, etc.