
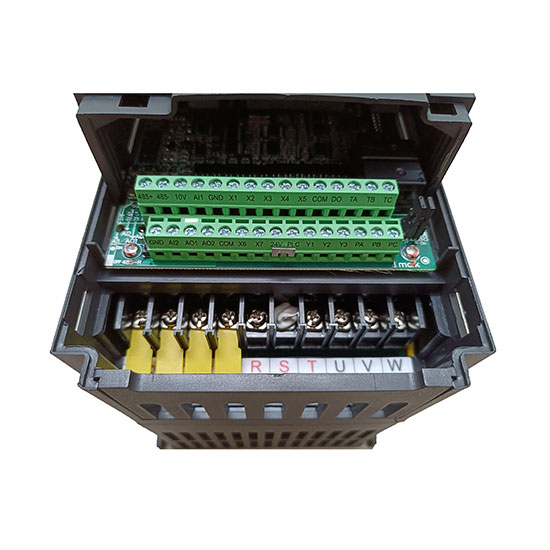






- Stock: In Stock
- Model: PEACO-FC110-2S/4T-0.75G
- SKU: PEACO-STVFD-1
Available Options
1 hp VFD to power the three-phase AC motor from single-phase/split-phase 220V-240V. Variable frequency drive draws a 7.5A rated input current from a power supply to deliver 2.5A to the 1-hp AC motor. Highly effective, stable operation, smooth start-up of AC motor, multiple controlling features, multiple safety protections, and CE certified with a 1-year warranty.
Peaco Support VFDs are suitable for single-phase and split-phase input power supplies.
Navigation: Motor Controls > Variable Frequency Drives >1 Phase to 3 Phase VFD > 1 hp VFD, Single Phase to Three Phase
Specifications
Basic Features | Model | PEACO-FC110-2S/4T-0.75G |
Code | G: Constant torque, P: Pump motor | |
Rated capacity | 0.75kW (1hp) | |
Rated input current | 7.5A | |
Rated output current | 2.5A | |
Input rated voltage | 220V | |
Input rated frequency | 50/60Hz | |
Output rated voltage | 380V | |
Allowable output voltage range | 320V~460V | |
Output frequency | Vector control: 300 Hz, V/F control: 3200 Hz | |
Adoptable motor type* | Squirrel cage induction motor, asynchronous motor (Contact us for Permanent Magnet Motor) | |
Control Features | Control mode | Open-loop vector control (SVC), Closed-loop vector control (FVC), V/F control |
Input frequency resolution | Digital setting: 0.01 Hz, Analog setting: Maximum frequency*0.025% | |
Carrier frequency | 0.5 kHZ-16kHZ, Automatically adjusted based on load features. | |
Torque control/Steady speed accuracy | ±5%(FVC)/ ±0.5%>(SVC), ±0.02%(FVC) | |
Start-up torque | G-type: 0.5 Hz/150%, 0 Hz/180% (FVC), P type: 0.5Hz (FVC) | |
Overload capacity | G-type: 150% rated current 60s, 180% rated current 3s , P-type: 120% rated current 60s; 180% rated current 3s | |
Ramp mode | Straight-line ramp or S-curve ramp, Four groups of acceleration /deceleration time with the range of 0.0s-6500.0s | |
DC braking | 0.00Hz - maximum output frequency, Braking time: 0.0s - 36.0s Braking action current value: 0.0% - 100.0%. | |
JOG control | JOG frequency range: 0.00Hz-50.00Hz, JOG acceleration / deceleration time: 0.0s-6500.0s | |
Build-in PID | Realizes process-controlled closed-loop control system easily. | |
Automatic voltage adjustment (AVR) | Maintain constant output voltage automatically when the main voltage changes. | |
Individualized Function | Safety self-inspection of power on peripheral equipment | Safety detection of peripheral equipment such as grounding, short circuits, and so on. |
Over-voltage and Over-loss speed control | Automatic limit of current and voltage during operation to prevent frequent over-current and over-voltage tripping | |
Fast current limit | Minimizing overcurrent fault and protecting frequency converter in normal operation | |
Common DC Bus function | Common DC bus functions of multiple frequency converters. | |
Quick key | User-defined shortcut menu | |
MF.K key | Programmable Key: Command channel Switching/forward and reverse running/JOG running function selection | |
Textile swing frequency control | Given the length control function | |
Timing control | Timing control function: setting time range 0h-65535hr | |
Running command sources | Running command sources | Three channels: operation panel, control terminal, and serial communication port. They can be switched over between these sources in various ways. |
Frequency sources | 10 frequency sources, such as digital setting, analog voltage setting, analog current setting, pulse setting, and serial communication port setting. They can be switched over these sources in various ways. | |
Auxiliary frequency command | 10 kinds of auxiliary frequency instructions. It can realize auxiliary frequency fine adjustment and frequency synthesis flexibly. | |
Input terminal | 7-Digital Input terminal, where X5 is compatible with high-speed pulse input. Suitable for PNP or NPN input mode. | |
2-Analog Input terminal 0-10V/0-20mA. Used either voltage or current input. | ||
Output terminal | 3-Digital output terminals and 2-Relay output terminals. | |
1-High speed output terminal DO, 0 kHZ-100 kHz square wave signal output, It can realize the output set frequency, output frequency, and other physical quantities. | ||
2-Analog output terminal 0-10V/0-20 mA. Use either as voltage or current output. | ||
Display and keyboard | LED display | Display monitoring parameters, output frequency, set frequency, bus voltage, etc. |
Keyboard lock and function selection | To realize partial or total lock of keys, define the scope of action of some keys, to prevent misoperation. | |
Protection function | Short circuit detection, input and output phase loss protection, overcurrent protection, overvoltage protection, under-voltage protection, overheat protection, and overload protection. | |
Brake unit | Build-in brake unit | |
Environment | Installation location | Indoor, free from direct sunlight, dust-free, corrosive gases, combustible gases, oil smoke, vapor, drip or salt, etc. |
Altitude | <1000m | |
Ambient temperature | -10°C~ +40°C (ambient temperature is 40°C-50°C , please de-rate to use) | |
Humidity | < 95 % RH, no water droplet condensation | |
Vibration | <5.9m/s 2 (0.6g) | |
Storage temperature | -20℃~+60℃ | |
IP level | IP20 | |
Pollution grade | PD2 | |
External Accessories* | Matched optional Brake resistance, input EMC filter, output EMC filter, input AC reactor, output AC reactor, energy regenerated reactor, harmonic filter, and sine wave filter (excluding VFD price). | |
Warranty | 1 year |
1. * denotes the parameters are optional or customized and please select every parameter in drop-down lists to complete your order.
2. 1-hp single-phase to three-phase VFD comes with a built-in brake unit. The customer must install brake resistance along with VFD when rapid deceleration is activated for the motor.
3. Please contact us for the external accessories catalog and price.
Variable Frequency Drive Wiring Diagram
A | H | D | W | B | Φ | Weight |
106.5 | 185 | 166.5 | 118 | 175.5 | Φ4.5 | 1.8kg |
KNOWLEDGE BASE
Why should I use a VFD?
- Reduce Energy Consumption and Energy Costs
VFD can make you manage the speed of the motor-driven electric equipment that is matched with the required speed of the load and you can reduce energy costs by controlling the motor with a variable frequency drive if your application doesn't need to run at full speed. No other AC motor control method allows you to achieve this.
Energy can be saved drastically by installing the VFD to regularize the speed.
- Increase Industrial Production Level
Most of the industrial equipment is equipped with motors in various forms where motors consume more than 50 % of the energy in industry. It can be reduced by installing the VFD along with the motor which regularizes the motor speed, and torque, and controls peak power demand.
- Extend Equipment Lifespan and Reduce Maintenance
Single-phase variable frequency drive can offer better protection for AC motors because of the over-heat, over-voltage, and low-voltage protection functions of VFD and can make sure the motor applications operate at the optimal speed. Therefore, there is less maintenance and longer service life for the equipment.