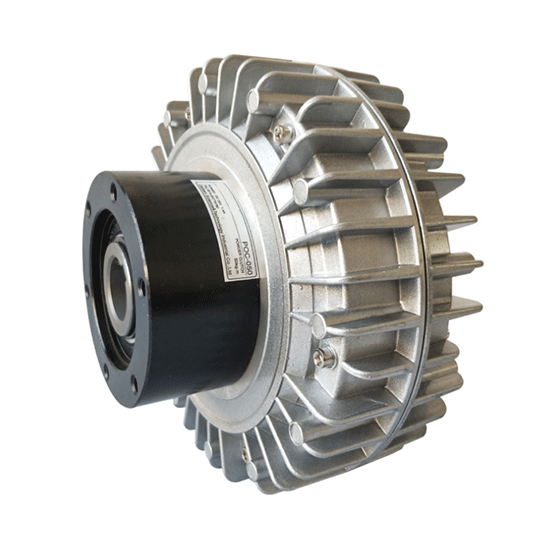
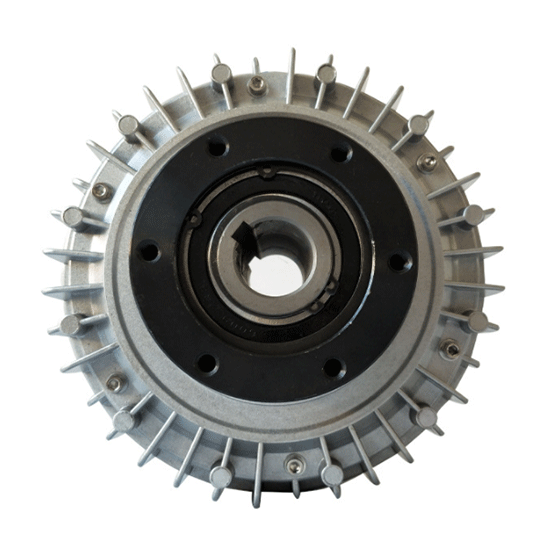
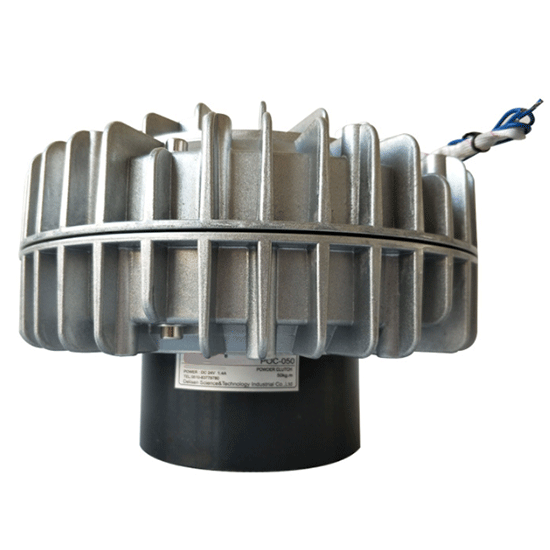
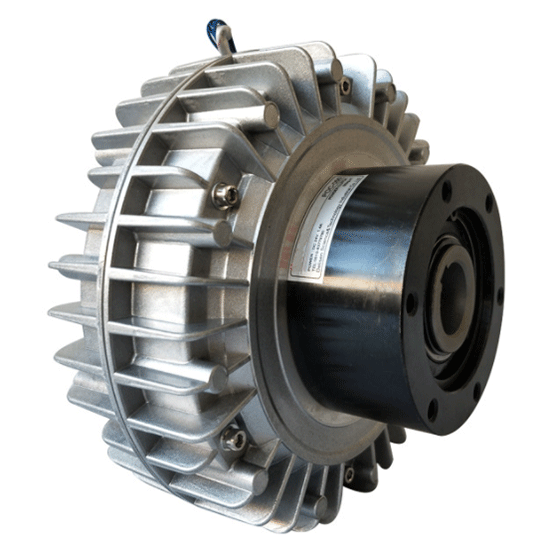
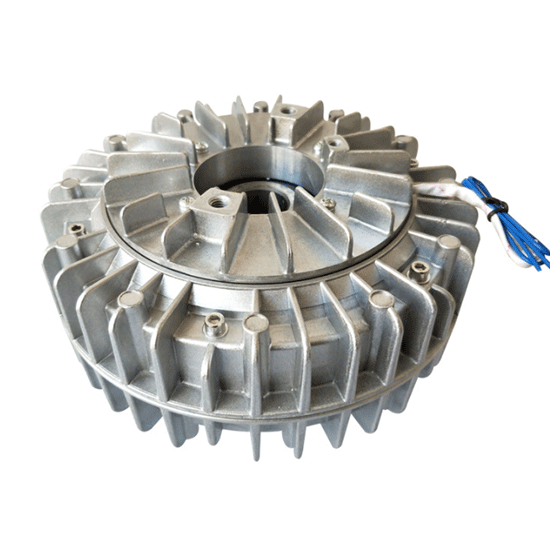





Magnetic Particle Clutch, Hollow Shaft, Shell Rotation, 6Nm-200Nm
- Stock: In Stock
- Model: PEACO-POC
- SKU: PEACO-POC
$454.58
Ex Tax: $454.58
Available Options
Free Shipping Worldwide.
By DHL/ FedEx/ UPS.
Lead Time 7-12 Days.
Mail Us for Lead Time of Custom Products.
MOQ 1.
Buy More Save More.
The magnetic particle clutch has a hollow shaft, shell rotation, a wide operating torque range from 6Nm to 200Nm, and a voltage DC of 24V. Mainly used for unwinding, rewinding, and tension control systems in machinery. High precision torque control, high quality, and competitive price.
Please note that the base is not needed for the small torque<100 N.m and is applicable for large torque ≥ 100 N.m.
For the magnetic powder clutch and brake catalog and user manual, please visit here Peaco Support Powder Clutch and Brake Catalogue.
Features
1. The excitation current has a linear relationship with the transmission torque. The magnetic powder brake's torque is linear with the excitation current. The size of the control torque can be adjusted at random by changing the size of the excitation current. The torque can be controlled over a wide range. Under normal conditions, the excitation current has a linear relationship with transmission torque within the range of 5% ~ 100% rated torque.
2. Stable rotational speed---the feature of torque. When the excitation current remains constant, the torque will be transmitted steadily and will not be affected by changes in speed. This feature is used in tension control, the torque can be controlled by only adjusting the excitation current, to achieve the purpose of tension control.
3. Effective heat sink and its load characteristics. When the friction part keeps sliding continuously, it will inevitably generate heat and even be destroyed. However, the PEACO magnetic powder clutch has a complete cooling device, which will not generate a lot of heat after long-term operation and has a long service life.
Specification
Model* PEACO- | POC-006 | POC-015 | POC-025 | POC-050 | POC-100 | POC-200 | |
Rated Torque | 6Nm | 12Nm | 25Nm | 50Nm | 100Nm | 200Nm | |
Capacity DC24V (75℃) | Current | 0.74A | 0.9A | 1.1A | 1.4A | 2.0A | 2.5A |
Power | 17.8W | 21.6W | 26.4W | 33.6W | 48W | 60W | |
No. of Hours Set | 0.04S | 0.04S | 0.06S | 0.09S | 0.14S | 0.3S | |
Moment of Inertia | Input Shaft | 2.70*10-3Kgm2 | 6.3*10-3Kgm2 | 1.2*10-2Kgm2 | 2.6*10-2Kgm2 | 7*10-2Kgm2 | 2.1*10-2Kgm2 |
Output Shaft | 5.0*10-4Kgm2 | 1.1*10-3Kgm2 | 2.3*10-3Kgm2 | 5.8*10-3Kgm2 | 1.5*10-2Kgm2 | 5.0*10-2Kgm2 | |
Maximum Speed | 1800r/min | 1800r/min | 1800r/min | 1800r/min | 1800r/min | 1000r/min | |
Weight of Powder | 14g | 25g | 39g | 60g | 117g | 255g | |
Item Weight | 2.7kg | 5.2kg | 9.0kg | 14.5kg | 37.0kg | 53.kg |
Dimension (unit: mm)
Model | POC-006 |
POC-015 |
POC-025 |
POC-050 |
POC-100 |
POC-200 |
|
L1 | 86 | 103 | 119 | 150 | 166 | 198 | |
L2 | 21 | 32 | 36 | 48 | 48 | 59 | |
L3 | 58 | 58 | 66 | 82 | 100 | 118 | |
L4 | 7 | 13 | 17 | 20 | 18 | 21 | |
L5 | 1 | 2 | 2 | 3 | 4 | 1 | |
L6 | 64 | 76 | 91 | 116 | 130 | 152 | |
L7 | 21 | 25 | 26 | 31 | 32 | 45 | |
D1 | 128 | 160 | 180 | 220 | 275 | 335 | |
D2 | 82 | 96 | 114 | 150 | 176 | 200 | |
D3 (g7) | 70 | 80 | 90 | 110 | 125 | 160 | |
D4 | 60 | 68 | 80 | 95 | 110 | 140 | |
D5 | 60 | 68 | 80 | 95 | 110 | 140 | |
D6 | 42 | 48 | 55 | 68 | 80 | 110 | |
R | M6*10L | M6*10L | M6*10L | M8*12L | M10*18L | M10*18L | |
Q | M4*8L | M6*8L | M6*8L | M8*12L | M10*18L | M10*18L | |
Axle Hole | d (H7) | 15 | 18 | 20 | 30 | 35 | 45 |
w (F8) | 4 | 5 | 6 | 8 | 10 | 14 | |
T (+0.2 0) | 16.5 | 20 | 22 | 33 | 38.5 | 49 |
Installation
Magnetic Particle Clutch Application
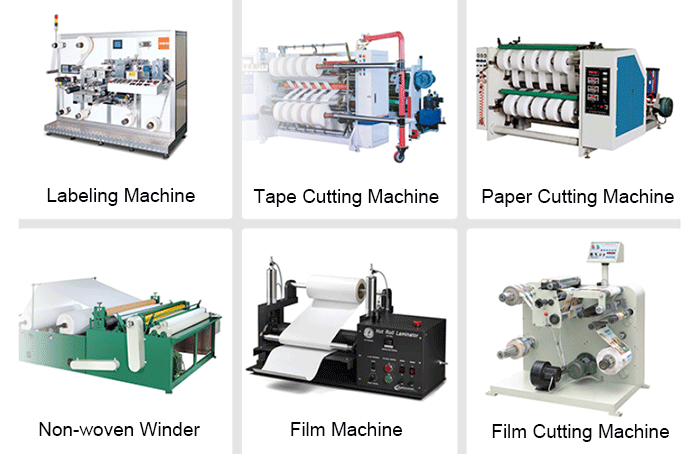
Magnetic Particle Clutch Package
KNOWLEDGE BASE --- Magnetic Particle Clutch Installation Instructions
- The magnetic particle clutch should be installed per the relevant mechanical requirements. The input side and output side of the torque cannot be reversed, otherwise it will affect the heat dissipation conditions and reduce the slip power. The magnetic powder clutch should be installed in the horizontal direction of the shaft and remember not to install it vertically.
- The air input by the forced air-cooled clutch must be degreasing and dewatering to prevent the powder from getting damp and damaging the coil, which will affect the life and performance of the magnetic powder clutch.
- If the magnetic powder clutch must be installed near the gearbox in some cases, an oil seal should be used to prevent grease from penetrating along the axis.
- When the clutch speed is below 15r/min, a weak excitation current of 3~5% should be maintained to prevent the magnetic powder from falling from the working surface. The minimum speed should be not less than 15r/min when speed speed-increasing mechanism is used.
- The surface temperature of the magnetic powder clutch during continuous operation should be below 80~90℃ for self-cooling, below 90℃ for water cooling, and below 70℃ for forced air cooling.
- The magnetic powder lifespan is 5000~8000 hours under the allowable slip power. When the torque drops below 30% of the rated torque, the magnetic powder should be replaced or supplemented, but the filling rate should be less than 100% to prevent excessive fever.
- The surface temperature of the water-cooled clutch should not be lower than 50℃ to prevent the condensation of water mist in the working cavity, reduce the flow of cooling water, and stop the operation to close the water circuit.
- The water inlet of the water-cooled clutch must be installed below the vertical direction. If it is not used for a long time, the water in the water cavity should be removed to prevent the clutch from moisture, rust, and some damage in cold areas. Additionally, stains and rust should be removed regularly.