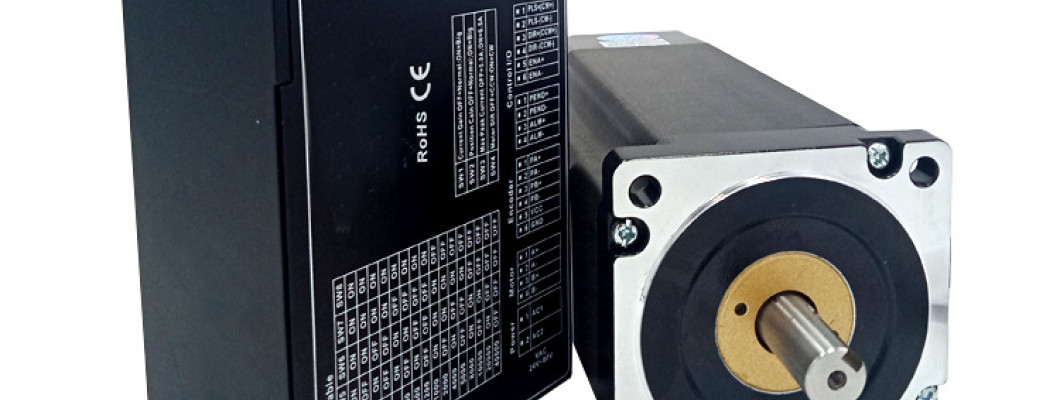
1. Preface
The automatic vertical packaging machine is suitable for packaging granular, short, and vermicelli-shaped materials, such as puffed food, peanuts, popcorn, oatmeal, melon seeds, jelly, sugar, salt, washing powder, etc. In the early days, the equipment adopted control mechanisms such as brake clutches. However, now it has developed into a control mechanism based on PLC and step/servo motors with variable frequency speed regulation.
Peaco Support has launched a special step control solution according to the current global vertical packaging machine status, which has been successfully applied and widely promoted in some packaging machine equipment companies in Europe and the United States. This solution uses our Peaco Support DSP86 stepper driver and Nema 34 (86*86mm) series stepper motor as well as the Peaco Support client's touch screen, PLC, inverter, variable frequency motor, and other components to form a complete stepping solution. The program used by the client has excellent performance and high-cost performance.
Figure 1: Automatic Vertical Packaging Machine
2. Working Process
Figure 2 is the schematic diagram of the working process of the vertical packaging machine. As shown in the figure, the entire equipment process is mainly classified into three parts: feeding, drawing die, and cutting. The whole process consists of a heat sealing cutter, stepping device, frequency conversion device, traction roller, bearing, and cutting top roller linkage.
During the packaging process, the material is fed by the stretching and feeding device. The plastic film passes through the film cylinder to form a cylindrical shape and the side is sealed by the thermal longitudinal sealing device. At the same time, the package is injected into the bag. The horizontal sealing mechanism detects the cutting length and position of the device according to the color code photoelectric for the equipment.
Figure 2: The Working Process of Vertical Packaging Machine
- Man-machine interface: The fixed length sealing and cutting or color label sealing and cutting, bag cutting length, bag delivery speed, etc. can be set on the touch screen and the interface. When fixed length sealing and cutting is selected, the other sealing and cutting is not working.
- PLC: Part of the core program to control the operation and coordination of other parts. According to the mechanical transmission ratio of the stepping mechanism, the electronic gear ratio of the stepper motor driver, the number of lines of the stepping motor encoder, and the circumference of the discharge roller, the PLC program calculates a certain number of pulses that the stepper driver receives and the stepper motor drives the discharge roller to rotate to bring out a certain length of plastic bag to realize fixed length control.
- Color/mark sensor: The sensor is responsible for time judgment and control signal sending.
- Main frequency conversion device: Responsible for the continuous up and down movement of the heat-sealing knife, at the same time, it is for controlling the bagging speed and efficiency.
- Stepping motor driver: The motor driver device is composed of a motor driver and a stepper motor. As the main movement mechanism, its main task is to complete the stepper motor position control (control of positioning accuracy), and strictly implement the pulse command control from the PLC. Meanwhile, it ensures the smoothness and fast response of its movement with frequent starting loads, thus, the feed speed of the stepper motor can meet the time requirement of the cutting knife running up and down. In a word, the performance of the stepper motor control system directly has some important impacts on the overall performance and quality of this equipment.
The Working Process of the Vertical Packaging Machine
a. The electric and temperature controller on the equipment controls the heater at the knife sealing place for heating.
b. The feeding frequency converter drives the feeding motor to transport the plastic film at a set speed. When the feeding sensor detects that the plastic films at the feeding end are enough, the feeding motor stops feeding.
c. The temperature reaches the preset value, the temperature control signal is turned on and the main inverter drives the main motor to control the up and down movement of the cutter and the sealing knife with the help of a mechanical transmission device.
d. Every time the cutter moves upward, the stepping signal is turned on for one time and the stepping motor drives the discharging roller to rotate once with the plastic film belt. While the cutter and the sealing knife are cut downward, the plastic bag is formed.
e. When the set numbers are enough or the stop button is pressed, the machine will stop after the current plastic bag is formed and the cutting knife and sealing knife will stop at the high place.
3. Peaco Support Stepper Motor Control System
The Peaco SUpport DSP86 stepper motor driver mainly drives the 2-phase hybrid stepper motor with 86*86mm and 110*110mm stepper motor sizing. The digital stepper motor driver is suitable for a variety of medium and large automation equipment, such as engraving machines, cutting machines, packaging machinery, electronic processing equipment, automatic assembly equipment, etc., especially well suited for those equipment that require small noise, and high speed.
There are 16 kinds of microstep fractions and the maximum number of steps is 51200Pulse/rev.
- The peak operating current range is 2.4A-7.2A.
- The output current has a total of 8 types and the current resolution is about 0.6A.
- With automatic half-current, over-voltage, under-voltage, over-current protection functions.
- The motor driver is powered by AC and DC and the recommended operating voltage range is 48VAC-80VAC (<90VAC and >24VAC).
- Signal Interface:
Pulse signal: CP+ is the positive end of the pulse input pin, and CP- is the negative end of the pulse input pin.
DIR signal: DIR+ is the positive end of the direction input pin, and DIR- is the negative end of the direction input pin.
Enable signal: ENA+ is the positive end of the direction input pin. This signal is used for enabling/disabling the stepper motor driver. High level for enabling the driver and a low level for disabling the driver. ENA- is the negative end of the direction input pin. Usually, it is unconnected (enabled).
- Motor interface
A+ and A- are connected to the positive and negative ends of the A-phase winding of the stepper motor. B+ and B- are connected to the positive and negative ends of the B-phase winding of the stepping motor. When the windings of A and B are switched, the direction of the motor can be reversed.
- Indicator lights
The stepper motor driver has red and green indicators. The green indicator is the power indicator. When the motor driver is powered on, the green indicator is on and the red indicator is the fault indicator. When overvoltage or overcurrent faults occur, the fault indicator is on. After the fault is eliminated, the red light is off. When the stepper driver is faulty, you need to power it on and enable the stepper driver again to get rid of the fault.
- Installation instructions
The external dimension of the stepper motor driver is 151*97*48mm and the installation hole distance is 143mm. Both horizontal and vertical installation are available, but vertical installation is recommended. When installed, it should be close to the metal cabinet for heat dissipation.
Figure 3: Peaco Support Stepper Motor Control System
4. On-site Debugging Results
The basic parameters of the packaging machine are as follows:
- Roller diameter: 36mm
- Bag length: less than 0.5mm
- Mechanical reduction ratio: 1:4
- Speed: 1500RPM
- The machine runs at the packaging speed of 40-60-80-120 bags/min and the packaging and filling are stable.
Taking a 200mm long plastic bag and a maximum packaging speed of 120 bags/min set in the machine as an example, the performance comparison between Peaco Support stepper motor drive and stepper motor and the ones of a brand is as follows:
Type | Stepper Motor Control System | |
Peaco Support | One Brand | |
Speed | 120 bags/min | 100-110 bags/min |
Accuracy | Higher | General |
Stability | Smoothy running. | Easy to produce vibration when starting and stopping. |
Noise | Small | Larger |
Price | Moderate | Lower |
Table 1 Comparison Test Data Table of Stepper Motor Control System between Peaco Support and a Certain Brand
The data in Table 1 shows that the stepper products of Peaco Support run more smoothly and efficiently than similar products on the market.
5. Summary
The vertical packaging machine is transformed and made based on traditional and old equipment to adopt the Peaco Support digital DSP86 series stepper control system, which has simple and easy operation, achieves automatic production, greatly increasing the production efficiency, improving the sealing and cutting accuracy, simplifying the mechanical structure. In a word, it is a cost-effective way to help enterprises to create more benefits.
Leave a Comment