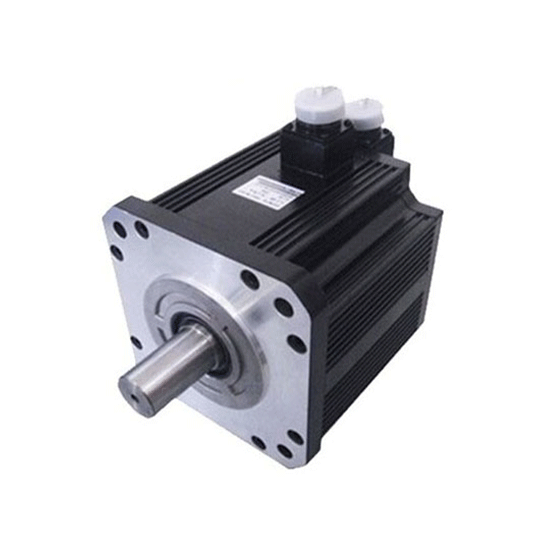
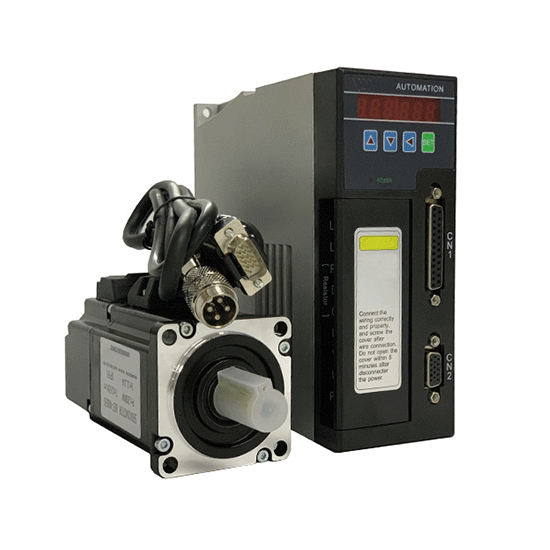
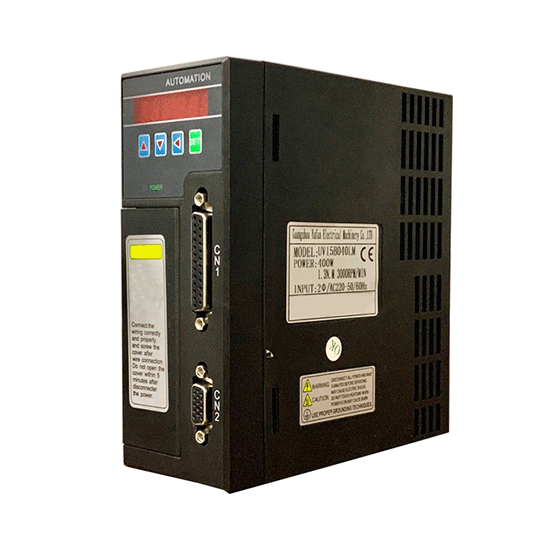
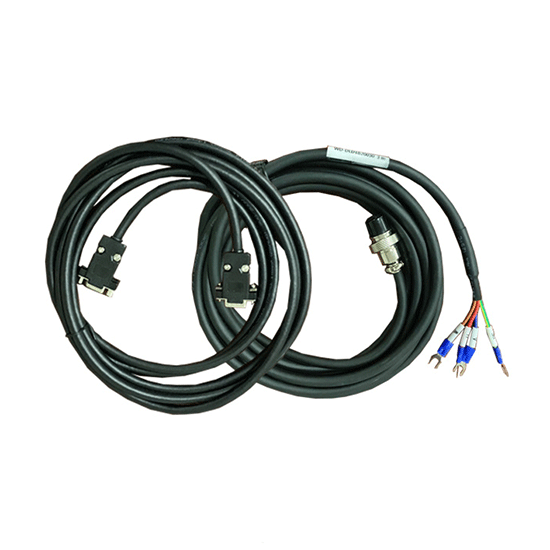




AC Servo Motor 3.7 kW, FLANGE 180mm, 35Nm 1000rpm
- Stock: In Stock
- Model: PEACO-180ST-M35010
- SKU: PEACO-180ST-M35010
$1,587.69
Ex Tax: $1,587.69
Available Options
Free Shipping Worldwide.
By DHL/ FedEx/ UPS.
Lead Time 7-12 Days.
Mail Us for Lead Time of Custom Products.
MOQ 1.
Buy More Save More.
AC 3.7 KW servo motor is equipped with 35.0 N.m holding torque, 70.0 N.m maximum output high torque, flange 180 mm and 1000 rpm high speed, providing encoders and brakes for option. Cost-efficient AC servo motor for various demands, such as printing equipment, medical equipment, laser machine, cutting equipment, automation equipment, robotic equipment. Low cost and high performance.
3.7 kW Servo Motor Specification
Motor Model | PEACO-180ST-M35010 | Line-line Resistance | 0.31 Ω |
Matched Servo Driver Model | PEACO-75B2 | Line-line Inductance | 3.28mH |
Frame Size | 180*180mm | Machanical Time-constant | 10.58ms |
Rated Power | 3.7 KW | Weight | 30.5kg |
Rated Voltage | 220V | Certificate | CE |
Rated Current | 16.0A | Warranty | 12 months |
Rated Speed | 1000rpm | Encoder Line Number (PPR) | 2500 |
Holding Torque | 35.0 N.m | Insulation Class | Class F (155℃) |
Peak Torque | 70.0 N.m | Safety Class | IP 65 |
Voltage Constant | 134 V/1000r/m | The Operation of Environmental Conditions | Temperature: 20℃~+40℃ |
Torque Coefficient | 2.2 N.m/A | Humidity: <90%RH (no dewing) | |
Rotor Inertia | 8.6x10-3 Kg.m2 | Application | Automation Equipment |
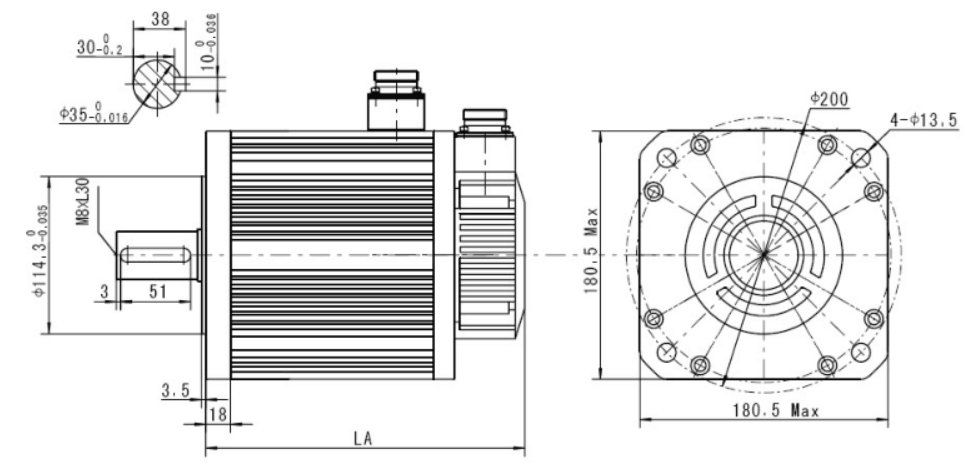
LA=292 mm (without brake), LA=382 mm (with permanent magnet brake), LA= 364 mm (with electromagnetic brake)
Input voltage of electromagnetic brake: DC 24V, Rated torque of electromagnetic brake: 50 N.m (with 35.0 N.m)
1. Installation/disassembly components coupled to the motor shaft end, do not hit shaft hard to prevent the other side of motor shaft encoder from damage.
2. Try to prevent its shaft from vibration and bearing damage.
B2 Model AC Servo Drive Features
- Control mode: position control mode, speed control mode, torque control mode, inner speed control mode.
- Feedback system: 2500 PPR incremental encoder or 17 bit absolute value encoder.
- RS484 Modbus communication is available.
- Encoder frequency divider can be set arbitrarily.
- The servo motor encoder has functions of speed and torque signal output (0 ~ 5V analog output).
- The new industrial IPM intelligent power module is adopted, small in size, strong overload capacity, high reliability.
- With excellent response and system rigidity, strong resistance to load disturbance and strong starting.
- Optimized braking unit is suitable for frequent start and stop.
- Easy and simple to operate, monitor and set parameters.
- Adaptive power: 4.3kW - 5.5kW.
B2 Model AC Servo Drive Data Sheet
Driver model | PEACO-75B2 | |
Output power | 4.3kW-5.5kW | |
Motor rated torque | 27N.m-48N.m | |
Feedback signal* | 2500 P/R incremental encoder or 17 bit absolute value encoder | |
Control mode | Position control, speed control, torque control, inner speed control, JOG control, trial run | |
Reborn break | Internal mount, External mount | |
Reborn break way | resistive load | |
Control Model | Speed frequency response | 250Hz or higher |
Speed fluctuation rate | <±3% (Negative load 0%~100%), <±2% (Power-10%~+10%) | |
Speed ratio | 1: 5000 | |
Pulse in frequency | ≤ 500 kHz | |
Position control | Control mode | 1. Pulse+Diretion 2. CW +CCW Pluse 3. Two phase AB Orthogonal |
Electrical gear wheel | 1-9999 / 1-9999 | |
Feedback pluse | Differential output can be set freely. | |
Speed control | Speed range | Speed range -3000~+3000rpm |
Speed signal | DC -10V~+10V | |
Speed range frequency | ±1% (Negative load change 0%~100%) | |
Torque control | Torque range | ±3 times rated torque |
Torque signal | DC -10V~+10V | |
Torque range frequency | ±1% (Negative load change 0%~100%) | |
Communication | RS484 Modbus communication | |
Earthing model | The shell of Servo drive to earth, earth resistance ≤ 0.1Ω | |
Monitor | Keyboard display | Speed. present position, order pulse accumulation, position deviation, torque, current, velocity, rotator absolute position, command pulse frequency, running sate, signal Input and output, mainboard temperature and alarm, etc. |
Analog value display | Speed. Torque, Current, Peak Torque, Rotator absolute Position | |
Protection | Over speed, over current, over load, under voltage, abnormal error, encoder error, abnormal power control, position error, over temperature, etc. | |
Working condition | Temperature | Working: 0℃~55℃, Storage: -20℃~80℃ |
humidity | <90%, no condensation | |
vibration | <0.5G (4.9m/s2), 10Hz-60Hz (No continuouse working) |
Winding and Encoder Connection Table
Encoder line number | 2500PPR | |||||||||||||||
Insulation class | Class F ( 155℃) | |||||||||||||||
Safety class | IP65 | |||||||||||||||
Using environment | Temperature: 0℃~+40℃ Humidity: below 90% RH (No dewing ) | |||||||||||||||
Motor winding plug | Winding Lead Wire | U (red) | V (yellow) | W (blue) | PE (yellow, green/black) | |||||||||||
Plug serial number | 2 |
3 | 4 | 1 | ||||||||||||
Encoder plug | Winding Lead Wire | 5V | 0V | A+ | B+ | Z+ | A- | B- | Z- | U+ | V+ | W+ | U- | V- | W- | PE |
Plug serial number | 2 | 3 | 4 | 5 | 6 | 7 | 8 | 9 | 10 | 11 | 12 | 13 | 14 | 15 | 1 |