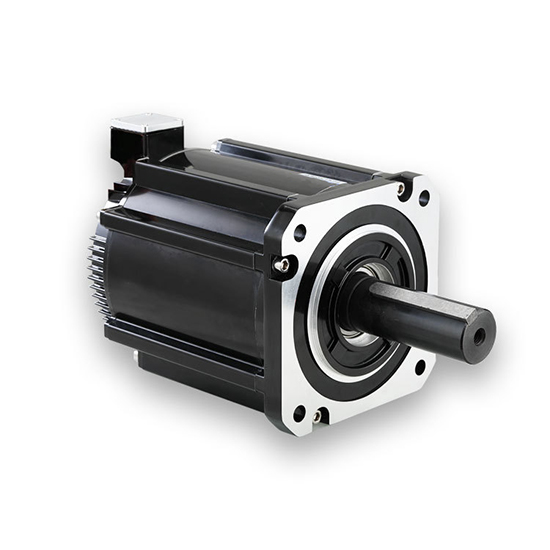
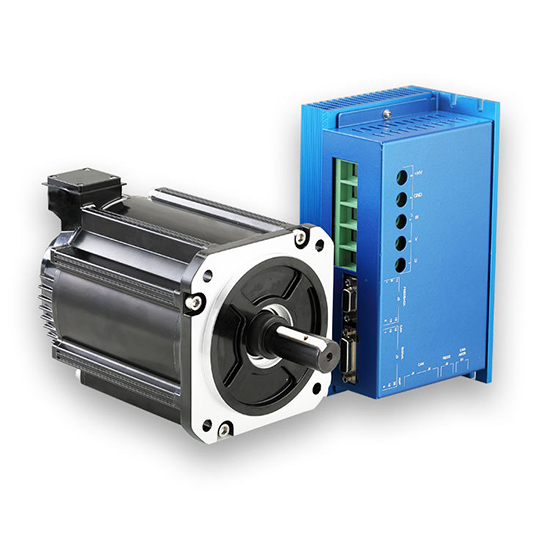
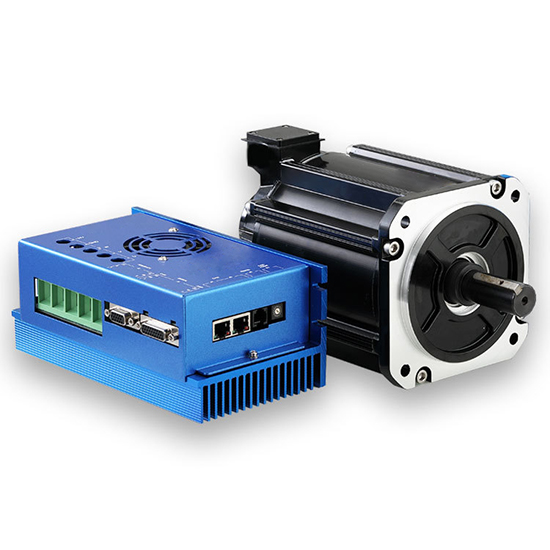



- Stock: In Stock
- Model: PEACO-D80M-04830
- SKU: PEACO-DCSERVO-1500
Available Options
Features
The DC servo motor control system, which is composed of a DC permanent magnet brushless synchronous servo motor and a corresponding servo drive, can be widely used in machine tools, textiles, plastics, printing and dyeing, printing, building materials, packaging, woodworking, chemical fields.
- The servo motor is composed of stator, rotor, feedback components, such as incremental photoelectric encoder, resolver, etc.
- The use of stator cores without shell allows large temperature gradients, high heat dissipation efficiency.
- DC servo motor has compact structure, high power density.
- Servo motor features small moment of inertia, fast response speed.
- Brushless DC servo motor comes with high-performance rare earth permanent magnetic materials, strong anti-demagnetization ability.
- DC servo motor with encoder has constant torque output in the entire speed range.
- 48 volt/ 72 volt servo motor provides high balance accuracy, stable high-speed operation, low noise, small vibration, fully sealed design.
- Servo motors are used in various industrial equipment, medical equipment, industrial tailoring machines, robotics, new energy, laser equipment, logistics automation, AGV vehicles, motion axes, and servo control systems. Such motors can convert voltage signals into torque and speed to control the mechanical components, so as to achieve the purpose of operation.
Specification
Model | PEACO-D80M-04830-48V | PEACO-D80M-04830-72V |
Rated Power | 1500W | 1500W |
Rated Voltage | 48V DC | 72V DC |
Rated Torque | 4.8N.M | 4.8N.M |
Rated Speed | 3000 rpm | 3000 rpm |
Rated Current | 42A ± 10% | 30A ± 10% |
Moment Coefficient | 0.11A ± 10% N.m/A | 0.17A ± 10% N.m/A |
Rotor Moment of Inertia | 2.4 ± 10% kg.m2x10-4 | 3.4 ± 10% kg.m2x10-4 |
Line Back EMF | 6.8 ± 10% V/krpm | 10.5 ± 10% V/krpm |
Line Inductance | 0.12± 10% mH | 0.12 ± 10% mH |
Line Resistance | 0.033± 10% Ω | 0.033 ± 10% Ω |
Motor Length (L) | 174 (165) mm | 174 (165) mm |
Motor Length with Brake (LB)* | 215 (205) mm | 215 (205) mm |
Weight | 6.5kg/7.3kg | 6.5kg/7.3kg |
Feedback Element X * (Optional) | Photoelectric incremental 2500 lines (E) / absolute value 17bit (A17) / rotary transformer (R) | |
Insulation Resistance | DC 500V,>20MΩ (F) | |
Operating Environment | -20℃~45℃, humidity -20℃~80℃ (No condensation) | |
Rotation Direction | Counterlockwise (CCW) | |
Protection Grade | IP65 (except for shaft opening), totally enclosed, self-cooled | |
Certification | CE | |
Warranty | 1 year |
Note: * denotes optional or customized parameters and you can select every parameter in drop-down lists to complete your order.
DC Servo Motor Dimension (Unit: mm)
KNOWLEDGE BASE --- Brushless DC Servo Motor
There are two main control methods for DC servo motors. One is armature voltage control, namely, when the stator magnetic field remains unchanged, the speed and output torque of the motor are controlled by controlling the voltage signal applied to the armature winding end. The other is excitation field control, that is, by changing the magnitude of the excitation current to change the strength of the stator's magnetic field so as to control the speed and output torque of the motor.
When the armature voltage control method is adopted, because the stator magnetic field remains unchanged, the armature current can reach the rated value and the corresponding output torque can also reach the rated value. As a result, this control method is the most convenient to realize. If the motor is driven by the actuator with a constant torque load, the armature current will not change before and after the speed adjustment. When the excitation field control method is adopted, since the magnetic field of the motor is close to saturation under the rated operating conditions, the speed of the motor can only be changed by weakening the magnetic field. Since the armature current is not allowed to exceed the rated value, the magnetic field weakens, the motor speed increases, but the output torque decreases and the output power remains the same. Therefore, such a method is also called constant power speed regulation.
The permanent magnet DC servo motor is usually used in the mechatronic servo system, so the armature voltage control method with the constant torque speed regulation is used , which is also consistent with the load characteristics required by the servo system.
The DC servo motor has features of rapid response, high precision and efficiency, wide speed range, large load capacity and output power and excellent control.
With the development of electronic technology, a new type of DC servo motor using electronic devices for commutation has appeared. It replaced the brushes and commutators of the traditional DC servo motor, so such a servo motor is called a brushless DC servo motor, which has high performance, longer service life because its commutator and brush parts have been replaced.