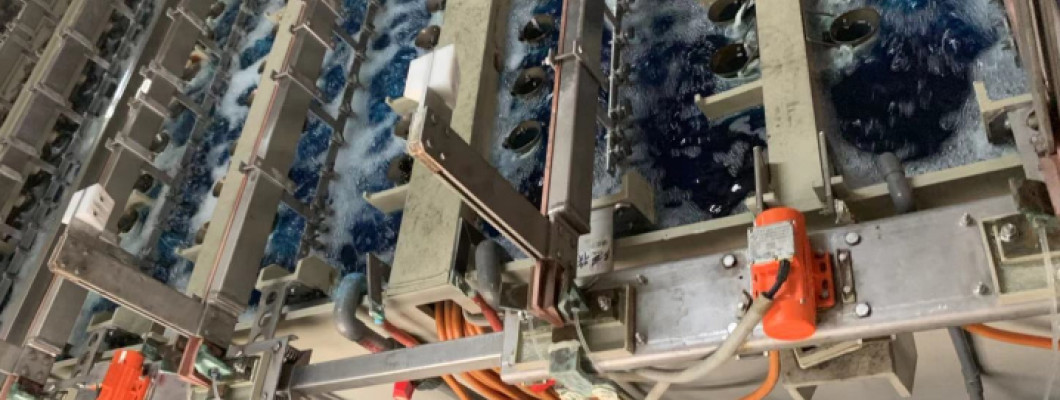
Improve the Bubble and Electroplating of the PCB Board
During the PCB electroplating process, the electroplating cylinder bulges, and there will be some tiny bubbles in the hole. It is difficult to remove these bubbles because of the affection of surface tension though the electroplating cylinder has the function of swinging mechanism, thus this way will easily cause bubble blockage. The smaller the bore diameter of the PCB board is, the more likely it is to happen. If the hole is blocked by a foreign object, the solution will not flow and exchange normally. What's worse, there will be no metal in the hole after the electroplating is completed.
To effectively improve this phenomenon, a vibration motor can be installed on the plating line. When the vibrating motor vibrates, it can improve the exchange frequency of solution in the hole and drive away bubbles. Additionally, it is also more difficult to exchange the solution in the hole in the process of PCB board manufacturing as the thickness-to-aperture ratio of machined plates increases, then the depth of electroplating decreases accordingly. However, the installation of industrial vibration motors can be a good solution to effectively improve the depth of electroplating.
Installation of a Vibration Motor
The vibration motor is generally installed on the base of the V-shaped seat. When the electrical vibration motor is running, the vibration can be transmitted to the electroplated conductive plate that will soak the fixed PCB board in different chemical tanks with the moving crane, which can effectively improve the depth of electroplating. The vibration motor can be installed on one side or both sides according to the different electroplating needs. Generally speaking, if the electroplated conductive plate is within 2m, then the one-side installation of the vibration motor is enough. The installation of a vibration motor on both sides is needed to transmit the vibration to the entire electroplated conductive plate if the length of this conductive plate is more than 3m.
Selection of Vibration Motor Power and Frequency
Both AC vibration motor and DC vibration motor can be widely used for PCB/circuit board/electroplating equipment. if you choose a 3-phase vibration motor, 3-phase asynchronous motor (AC vibration motor) is recommended, it features 51 kg vibration force, 50W input power, AC-rated 110V/220V voltage, and 50Hz frequency. What's more, if a single-phase vibration motor is needed, 1 phase asynchronous motor or 50W DC brushless vibration motor is our recommendation. A variable frequency drive can be installed to adjust 20Hz to the basic frequency.
Peaco Support micro-vibration motors have increasingly significant effects on improving air bubbles and improving deep plating ability during the PCB electroplating process. The AC vibration motors and DC vibration motors have been widely used in various large-scale PCB circuit board production lines worldwide. Such small vibration motors have a wide range of applications, including feeding, conveying, screening, and separation processes, and automatic vibration molding in the chemical industry, food industry, pharmaceutical making, packaging, and other industries. Peaco Support industrial vibration motors have reliable quality and the vibration motor price is very competitive. For more information about vibrating motors for sale, please contact us.
Leave a Comment