20 May
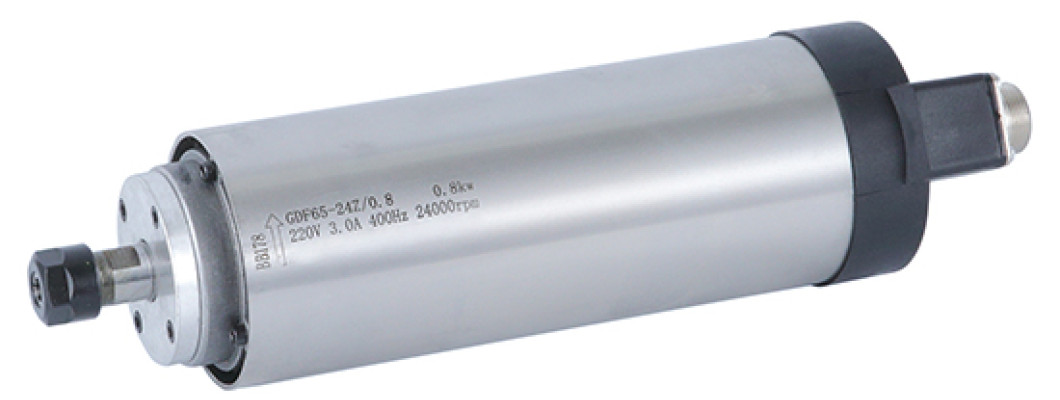
0 Comment(s)
313
With the development of science and technology in modern times, milling machine is such a machine tool equipment that is widely used in industrial production. It is definitely necessary to pay much more attention to the maintain the spindle motor for metal milling in the production process if users would like to extend the service life of the milling machine.
How to Maintain Milling Machine Spindle?
Lubricating oil is often used to reduce the operating temperature of the bearing. There are usually two types of lubrication, namely oil-air lubrication and oil-circulating lubrication. The following points should be paid attention to when users are lubricating the spindle bearings.
1. When operators are using oil circulation lubrication, it is necessary to ensure that the oil amount is sufficient in the constant temperature oil tank of the spindle.
2. The oil-air lubrication is a different way compared with the oil-liquid circulation lubrication. 10% of oil amount of the bearing space capacity is only needed.
There are some outstanding advantages of circulating lubrication. With the lubrication for spindle bearings, friction and heat generation can be reduced. Additionally, it can absorb some heat of the main shaft assembly.
There are also two ways to lubricate spindles: oil mist lubrication and spray lubrication. To reduce the bearing heat and effectively control the heat source are the primary cooling methods of the main shaft.
The sealing of the spindle components can not only keep dust, chips and cutting fluid from entering the components, but also prevent the leakage of lubricating oil. There are contact and non-contact sealing for the spindle components.
On the one hand, when adopting contact sealing - linoleum ring sealing and oil-resistant rubber sealing, users are supposed to pay attention to check their aging and damage. On the other hand, when non-contact sealing method is used, it is important to ensure that the returning oil can be drained as soon as possible and the oil-returning hole must be unobstructed in order to prevent leakage.
In a word, good lubrication effect can reduce the working temperature of the bearing and prolong its service life. it is very important for users to ensure that oil circulating lubrication can be used when it is at low speed and oil-air lubrication can be adopted when at high speed.
However, when grease lubrication is adopted by users, the usage amount of the spindle bearing is usually 10% of the bearing space volume. Excess grease is should be avoided, because too much grease will aggravate the spindle heating. With regard to oil circulation lubrication, it is a good way for users to check the spindle lubricating oil tank every day during operation. If the oil amount is not enough, users need to add lubricating oil timely. At the same time, operators needs to check whether the temperature range of the lubricating oil is appropriate, either.
How to Maintain CNC Engraving Machine Spindle?
CNC engraving machine spindle is an electric spindle used for high-speed milling, engraving, drilling, stamping. The spindle is the core component of the CNC engraving machine. If people use it without any maintance for a long time, the spindle is easily damaged, which will lead to your work delay and high repairing cost. Therefore, it is very necessary for users to perform daily maintenance on the spindle of the CNC engraving machine.
1. The CNC engraving machine spindle is the equipment that deals with the most processed workpieces and wastes, thus, it is very important to clean the spindle . After the CNC machine tool has been running for a day, the operator should use a vacuum cleaner to clean the spindle motor as well as motor rotor end terminals to prevent some waste from accumulating on the rotor end and terminals, so as to prevent waste from entering the bearing and accelerating bearing wear.
2. The user should develop the habit of cleaning the spindle collet and other parts after unloading the knife.
3. It is a must for users to clean the tool and spindle collet when installing the tool is under process, which can greatly prolong the service life of CNC spindle motor.
4. Whenever installing and changing the tool, users are supposed to unscrew the cover and it is forbidden to directly use the insertion method to replace the tool.
5. Chipped, corroded or worn toolholders should not be used during operation. Otherwise it will lead to damage the spindle.
There are two types of CNC engraving machine spindle, air cooled spindle motor and water-cooled spindle motor. Therefore, the spindles maintenance varies from diffrent spindle motors in addition to the basic maintenance mentioned above.
How to maintain water cooled spindle motor?
1. Since the water-cooled spindle motor adopts water circulation cooling, it is necessary to replace the cooling water frequently to ensure the water is clean. In the meantime, users should pay attention to the spindle motor temperature during processing. If the temperature rises, users need to check whether the water circulation is normal or not. In a word, it is a good idear to replace cooling water in time.
2. Because of the cold weather in winter, the cooling water should be dealed with timely in order to avoid the damage to the spindle after users finishes the working with the CNC milling machine, which can prevent the water pipe or water tank from freezing. There are also an alternative way that you can choose coolant instead of water, which is not easy to freeze and has a good cooling effect.
3. It is strictly forbidden to turn on the spindle motor without cooling water. Only under the premise of normal cooling, the spindle motor can work in good condition.
4. It is very necessary to frequently clean the tank, pipes, inlet/outlet and other parts through which the water flows to remove any blockages. If there is dead bend in the pipeline, water flow or dirt will block the pipeline, which will cause the spindle motor to fail to work properly and the processing will be affected.
Leave a Comment